Table of Content
The average starting price range for constructing a new modular home is $55 to $75 per square foot. Compare that to the average starting sale price of a traditional stick built home coming out to $250,000, and it’s no wonder that so many happy families decide to settle into a beautiful modular home in Maine. The fresh, crisp air and abundant wildlife make the choosing the right modular home builder in Maine an easy decision. The Old Line State, often the nickname given to Maryland, is a great place to buy a new modular home. So if you are in the market for a new modular home in Maryland, look no further than the beautiful eastern, culturally rich state with so much American History behind it and a flavor for any palate. Maryland modular home builders, such as Commodore Homes, Excel Homes, and Professional Building Systems are amongst some of the great modular home retailers servicing Baltimore, Silver Springs and beyond.

Clean the dirty markup with the big button which performs the active options in the list. When a clean operation is performed the program might add a paragraph to the text, containing a backlink to one of our partner sites. Paste the document you want to convert in the Word Editor, then switch to HTML view using the big tabs at the top of the page to generate the code. Word HTML is the perfect tool to edit the source code of WordPress articles or any other content management system when their built in composer doesn't provide all functionalities we need. Compose the content right in your browser window without installing any extension or plugin to handle the syntax highlighting and other text editing features.
Public Service
For itemized contribution and expenditure reports on state ballot measures, go to theCA Secretary of State’s ballot measure page. Prefabs were also built in the First World War such as the still occupied houses in Austin Village, Birmingham. Despite the intention that these dwellings would be a strictly temporary measure, many remained inhabited for years and even decades after the end of the war. A small number are still in use in the 21st century, but more and more are being demolished. In 2011 it was announced that Britain’s largest remaining prefab estate of 187 homes in Lewisham, South-East London, is to be redeveloped except for six homes.
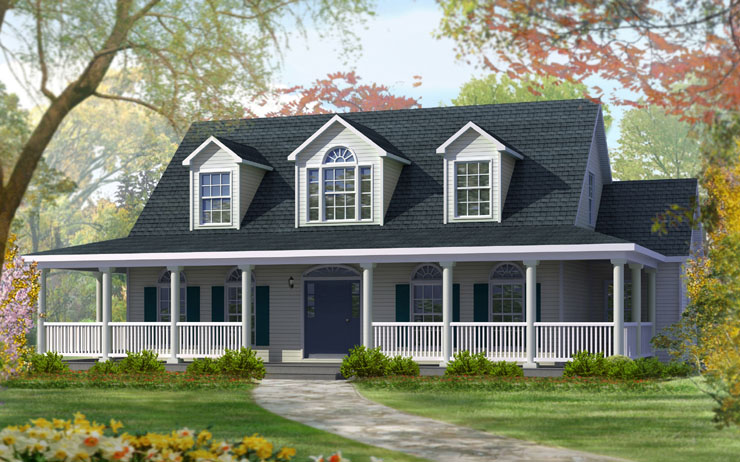
Trained craftsmen work together every step of the home building process to make sure we construct homes strong enough to last a lifetime. In the United States, several companies including Sears Catalog Homes began offering mail-order kit homes between 1902 and 1910. Forest Service, put extensive research into prefabricated homes in the 1930s, including building one for the 1935 Madison Home Show.
Shop Houses
The examples and perspective in this section deal primarily with the United Kingdom and do not represent a worldwide view of the subject. Mobile homes, or trailers, are built on wheels, and can be pulled by a vehicle. They are considered to be personal property, and are licensed by the Dept. of Motor Vehicles. They must be built to the DMV code, and pass inspection for licensing. Manufactured homes are built onto steel beams, and are transported in complete sections to the home site, where they are assembled. Wheels, hitch and axles are removed on site when the home is placed on a permanent foundation.
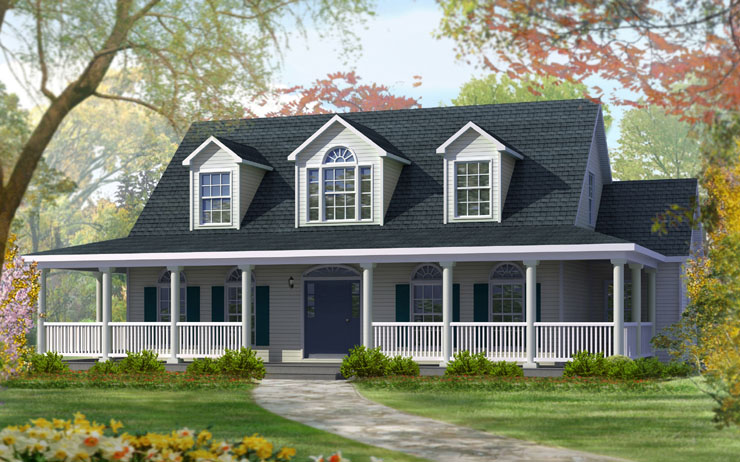
In many cases, modular construction (off-site) is less costly than traditional site-built methods. We are able to provide a fair price for materials, along with excellent fit and finish, without compromising quality. Our modular homes are built by experienced craftsmen and transported to your site for completion by a GHC-authorized builder licensed in your area. Our system yields high-quality structures with fewer time delays than our “site-built” counterparts. GHC methods reduce waste going into landfills, while providing an extremely stable structure.
Aeris Communications, Inc.’s Acquisition of Ericsson’s IoT Business
Additionally, we protect our materials from the elements, unlike “site-built” options, where materials may be exposed to the sun, rain, snow, wind, and theft. With the housing market continuing to grow, home costs are becoming much more difficult for the average consumer to afford. This has led to a variety of new, more cost-effective metal building homes design options. ENERGY STAR provides its active partners the opportunity to utilize the ENERGY STAR brand in promoting homes that earn the ENERGY STAR label. Modular manufacturing plant and builder partners must adhere to ENERGY STAR's Brand Brand Book when promoting ENERGY STAR certified modular homes. These guidelines describe how the ENERGY STAR name and marks may be used in promotional materials.
At ModularHomes.com, we give you the ability to discover why a new modular home is the perfect choice. Today’s modular homes are built in climate-controlled, factory environments. This protects the building process and the workforce from wind, rain, and snow, so their construction can’t be delayed by inclement weather like traditional homes. Home builders use modern modular construction techniques and technology to build homes precisely and quickly, and build homes from interior to exterior to add unique features like improved insulation. In fact, modular and manufactured homes are tremendously energy efficient, adding to their already excellent value by lowering their cost of ownership. These procedures must also include reporting requirements for builders to report their ENERGY STAR activity to the QAP.
Custom metal buildings are moving in the same direction by making use of containers into the building package. A third–party consultant must inspect, test and certify homes installed and completed by the builder on site, as well as report qualifying homes to the QAP. The QAP approves and monitors this third party, who must possess qualifications appropriate for the task as defined by the QAP. Site testing follows a sampling protocol, reflecting the fact that the manufacturing plant has been certified and has demonstrated the ability to consistently produce homes that comply with ENERGY STAR requirements. Simplex custom built modular homes range from Ranch, Two Story, Cape, Townhouses, Duplex, Triplex, Campus Housing and Light Commercial.
In 2010, Bali exported 98,417 prefabricated houses, but in 2011 the region only exported 5,007 units due to the global economic slowdown that affected a number of export destinations. These Balinese prefab houses are well known for their artistic design and practical value. After the World War II until 1948, Sell-Fertighaus GmbH built over 5,000 prefabricated houses in Germany for the occupying force of the United States. Panelized homes are generally considered a halfway between more traditional site-built home and more manufactured prefabs, with the flexibility of site-build and efficiency of prefab. We use quality materials, and have superior fit and finish – all at a cost that will likely be lower than a traditional site built home. Metal building manufacturers have sprung up offering a wide array of metal home kits and custom floor plan options to the everyday consumer.
We offer a wide selection of options, however, if you don’t see what you want, let us know. It supports the most common WYSIWYG features but you can't save your document. To save you'll have to copy the results in a desktop editor and save there.
Downing Hydro AB announced the acquisition of a 14 GWh run-of-river hydropower portfolio of seven assets with significant reservoir capacity... Simplex Industries, a leader in the modular industry and one of the region’s leading employers, has announced a succession plan in which long-time Vice President David Boniello will become President of the company on January 1, 2022. The announcement was made by current President and managing partner Patrick Fricchione, Jr., Fricchione will remain Chairman and CEO of the company. If you have questions about your Questia membership, customer support will remain available through the end of January 2021.
No comments:
Post a Comment